Watching Paint Dry
The unexpectedly interesting story of car coatings and what they tell us about the modern world
What follows is, on the surface at least, a story about paint, which will sound terrifically boring but, without wishing to give the game away, this isn’t really just about paint.
In fact, it’s about everything. Look at the world from the vantage point of car paint and you begin to see various strands of the 20th century storyline unfurling: the early days of mass production and the modern factory, the ascent of mass consumption, the rise and fall of economic growth, all the way through to today’s “productivity puzzle” economists are trying to get their heads around.
Honestly: car paint is such a fascinating topic that I’m surprised so little has been written about it. Then again, something similar goes for a lot of the obscure stories from the Material World, the book I’ll be publishing later this year. What follows is a side story I couldn't quite fit into the book, but if it whets your appetite, please pre-order a copy - doing so, even some months in advance, makes an enormous difference. In the meantime… here’s a story about car paint.
Like most stories about the car industry, this one probably ought to begin with Henry Ford. After all, one of the most famous things the godfather of mass production said of his most famous car, the Model T, was that the customer could get it “in any color he wants, so long as it’s black”.
Painting the Model T in black alone was one of those decisions that stood for a lot more than a choice on a colour palette. By narrowing his colour selection down to one and only one, Ford was able to streamline the production process, speeding up the rate at which cars would progress through the plants at Detroit.
Time, after all, is money, and the quicker you can paint (and dry) a car, the sooner you can get it into the hands of customers and the sooner it is out of the way of the other cars steaming down the assembly line. And painting a car takes time: considerably more time, as it happens, than actually making a car.
Up until 1914 it took Ford about 12 hours to assemble all the relevant parts into a finished car. But painting a car was time-consuming, especially back in the first decades of the 20th century. Each coat of paint on the Model Ts had to be brushed or dipped on and allowed to dry before the next layer went on. While the duration of assembly was initially measured in hours, the duration of painting was measured in days or even weeks. Cars would stack up, thousands of them, in warehouses as the chemicals in the paints slowly cured and turned solid.
Very little attention is paid to car paint, for understandable reasons. When you think of cars you think of the engine with all its moving parts. You think of the body and the camshaft and the wheels, all of which are part of the finely tuned mechanism endowing it with movement. The paint seems almost like an afterthought.
Except that it is anything but. Paint turns out to be an incredibly important element of car manufacture, partly for the reasons Ford ran into: for many years it was the lengthiest of all the processes in a car plant. These days, where we use enormous ovens to cure and dry car coatings, it is comfortably the most energy intensive and carbon intensive parts of making a car.
And it is partly because car coatings also serve an absolutely essential role, protecting the metal in a car from corrosion and slow motion disintegration. It is thanks to modern car coating techniques that you are so much less likely to see rust under the hoods or door arches of cars produced in the past couple of decades. How? We’ll get to that in a moment, but for the time being, back to the era of Henry Ford.
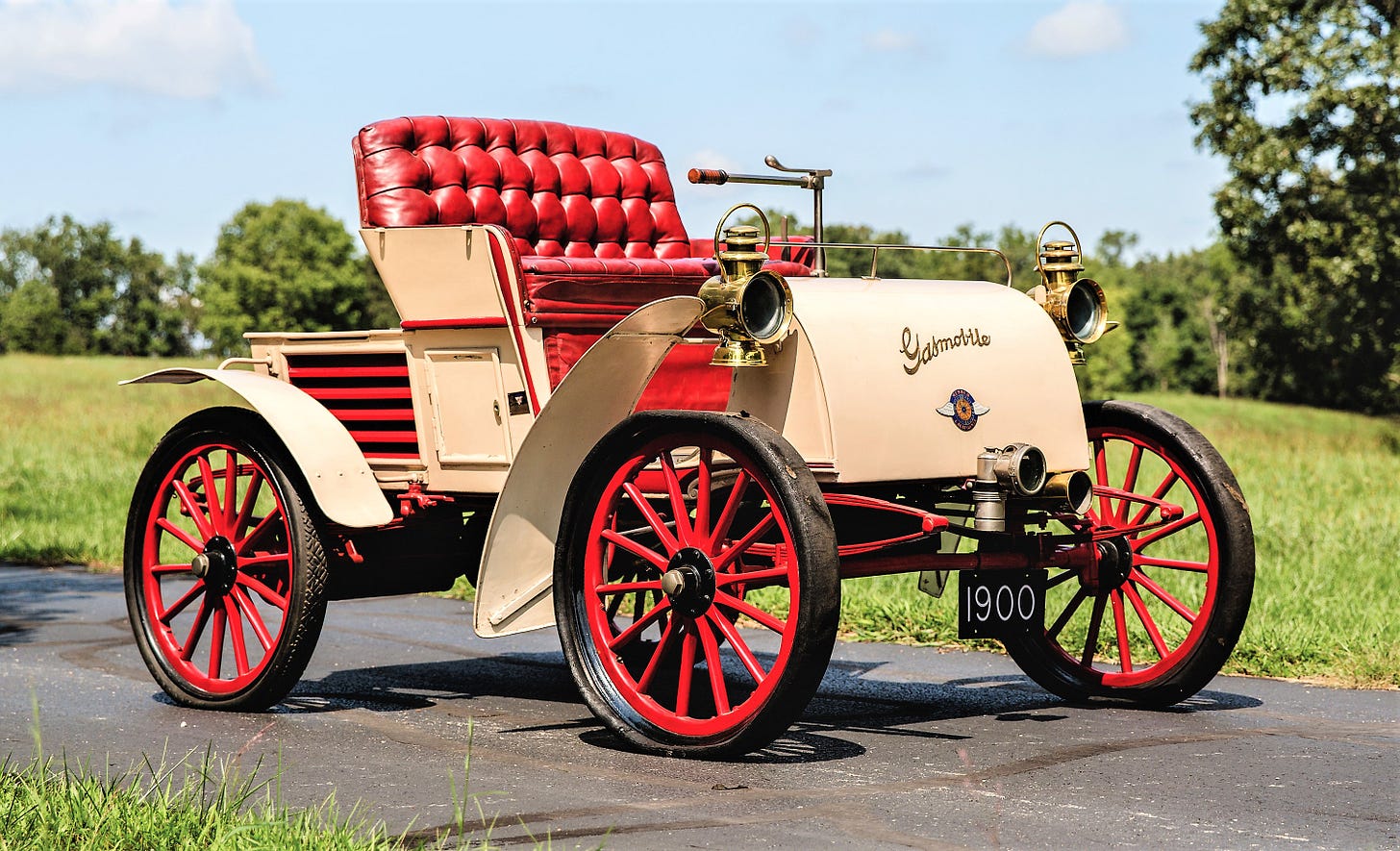
Before Ford and the Model T, cars came in all sorts of fantabulous colours. They were painted in the same kinds of bright coatings as horse-drawn carriages, but one problem was that these paints would fade rapidly, meaning you would have to get them repainted regularly. Another was that the painting would take weeks. So painting was one of the critical nuts for Ford to crack if he was going to churn out the quantity of cars he intended to.
And he spent much of his career attempting to crack that nut. He commissioned chemists to work at the paint formulas, he researched ways of drying the cars in gigantic ovens and, as we all know, he narrowed down the number of available colours to one.
The conventional wisdom is that Ford decreed that all Model Ts should be black because that was the fastest-drying of all colours. Actually, this mythical version of history isn’t entirely accurate according to an exhaustive history by Trent Boggess. Moreover, even in 1909, the same year that famous Ford quote dates from in his autobiography, you could still buy a Model T in red, grey, dark green or midnight blue. Only in 1915, when Ford moved to a new assembly line, did those colours get replaced with black.
It was certainly simpler to paint all the cars the same colour, and the black paint, made mostly of a varnish derived from vegetable sources, seemed to be harder wearing than other colours. Part of the secret to this was that the paint also contained a kind of asphalt. But the asphalt was so dark it was nearly impossible to turn it any colour other than black. So, black it was - partly because keeping it to one colour was simpler and quicker, partly because it was nigh on impossible to make an asphalt-based paint look anything other than black. Though while we’re on the topic it’s worth noting that actually there wasn’t a single black paint but 30 different types of black paint: some which could be baked in an oven, others that would have to dry in the air, some for the metal parts, some for the heel boards, the toe board, the seat bottoms and so on.
But despite all his efforts, despite countless innovations in paint technique, despite reducing the painting and drying time from weeks to days, Ford struggled to solve the paint problem. It was still the single biggest hindrance to mass production well into the 1920s. That brings us to the invention of something called pyroxylin, or as it was later trademarked, Duco.
Duco was a substance made from nitrocellulose by the chemists at DuPont. Nitrocellulose had been one of the critical ingredients in the development of explosives and, of course, celluloid movie picture film, but arguably its most revolutionary application was in car paint. For Duco had superpowers.
It was a lacquer resin which could dry far, far quicker than the paints Ford was using. While his paints might take a day or so to dry, Duco could dry in about two hours. Moreover, unlike Ford’s asphalt-heavy paints, Duco could be formulated in many wonderful, bright colours.
DuPont signed a deal with General Motors and in 1924 Duco was introduced on the company’s entire line of cars. It was a revolution in two dimensions. First, GM and DuPont had cracked the mass production nut which had always eluded Henry Ford: no longer did cars need to stack up in car lots to dry for days at a time: they could roll off the production line only a few hours after being painted. Second, the astounding range of colours changed the nature of car consumption.
Indeed, if you were looking for a start date for the era of conspicuous consumption and “planned obsolescence”, you could hardly chose a better moment than this one. Under Alfred Sloan, GM shifted the model of car marketing. Models were sold on their attractiveness. New colours were introduced each year to wow consumers. Alongside gradual changes to car features each year, Sloan championed an approach of “dynamic obsolescence” which would put pressure on consumers to upgrade their cars routinely rather than run them into the ground. Car paint, more specifically Duco, was one of the critical vectors in this strategy.
Except that only a few years after it was invented, Duco was already out of date. Soon enough chemists developed glycerophthalic resins (or alkyds, as they’re more commonly known) which had three times more solid matter than cellulose lacquers like Duco, meaning you could reduce the number of coats you needed, and hence further cut the time on the production line. Ford embraced alkyds in the late 1920s, and so the race between the two car giants intensified. Even as they battled it out in showrooms and in their massive plants, Ford and GM were battling it out on the chemical arena too.
Which brings us to a really important point - an overarching point which echoes through Material World. The influence of the chemical industry on modern products is astoundingly important, yet it’s one of the least appreciated and most rarely told stories in the modern industrial pantheon. We hear much about the mechanical engineering which went into steam locomotives and internal combustion engines but far less about the chemical engineering which allowed car manufacturers to keep their production lines turning.
Yet over time advances in paint chemistry allowed car manufacturers to drastically reduce the time it takes for paints to dry. The composition of those paints changed drastically too: from ingredients derived from wood and plants to molecules extracted from oil and gas. Car paints went from being made of vegetables to made of petrochemicals, and along the way they became significantly more hard-wearing and effective. Today pretty much all car paints are derived from oil and gas. And over time the length of time it has taken to paint and dry the cars has fallen.
Indeed, if you were to plot this - time taken to paint and dry a car versus the date - on a chart, then you get something that looks a little like this:
There are a few striking things about charts like these. The first is that you can see how over time humans have become better and better at doing things more efficiently. But the biggest gains often happen at the very start. The second is that you’ve probably seen similarly-shaped charts before. Here, for instance, is a chart from Hannah Ritchie (with a rather more solid dataset behind it) showing the evolution of battery prices over time:
You could do something similar with all sorts of different products: the price of wind turbines, of iron and steel nails, of computing power. One of the critical lessons which spans Material World, and which has been explained in great depth by people like Azeem Azhar, is that over time humans get better and better at making things, which tends to bring the time it takes us to make things (and for that matter the prices we charge for those things) further and further down.
Perhaps by this stage you are starting to see why car paint is actually a lot more interesting than many might assume: it’s a microcosm of human achievement. But it’s interesting for another couple of reasons too. The first is something you can’t really see in the chart above.
These days pretty much all cars are painted not just with spray paint (usually applied by robots) but through a process known as electrodeposition coating. The car body, which has already been coated with something called a “phosphate layer” to cover the naked steel (or aluminium) is attached to electrodes which give it a negative charge and dunked into a bath of positively charged liquid paint. Thanks to the magic of electricity, the epoxy coating in the water attaches itself to every single surface on the car body. Once the body emerges from the ED tank it is completely covered in a greeny-grey coat.
Electrodeposition isn’t the only process involved in painting a car these days. After that the edges get sealed with a silicone seam sealer and the body is sprayed with primer (which also helps flatten the steel and improve the reflection) and then covered with a couple of top coats which apply the colour. But electrodeposition, a technique introduced in the 1970s, has completely transformed the nature of car coatings because it is far more effective at protecting cars from rust. This, more than any other innovation in recent history, helps explain why these days cars are far longer-lasting than their older cousins.
None of this is apparent from the chart above. But even as the time taken to paint a car has decreased (hence increasing the potential efficiency of carmaking), the quality of the car coating has increased. Not only are we getting faster at making things, the end products are invariably far better too. One of the reasons why I so enjoyed the process of researching and writing Material World is that while macroeconomics (my usual territory) tends to treat productivity as an abstract force, actually when you get down into the nuts and bolts of how the world works - of how we turn simple substances into incredible machines and products - you see productivity everywhere. You see the world becoming a better, more efficient place. So it is with car paint.
The other thing you don’t see in the chart above is that over time, paints have become cleaner too. Earlier acrylic car lacquers produced significant amounts of volatile organic compounds which were emitted into the atmosphere both during the manufacturing and, slowly, thereafter too. While much of the effort in the early days of car paint was all about getting that curve in the chart above down - reducing the painting and drying time - these days far more effort is being expended in trying to remove solvent use and, at the same time, trying to reduce the time cars spend in ovens, most of which are still gas-fired.
This speaks to another broader pattern which you see writ large in everything from air travel to computer chip manufacture. For much of the 20th century most research and development was aimed at making things faster. But in the past few decades much of that R&D has been devoted to making things cleaner. Planes no longer fly as fast as they once did in order to conserve fuel and reduce emissions. What counts as progress in computer chip design and manufacture these days is not just speed but efficiency (in other words reducing relative power consumption).
Extrapolate this across the economy and perhaps you start to see an issue. If you measure productivity in terms of the speed at which a car plant can churn out cars then you might be a little disappointed by the progress over the past couple of decades. That line in the chart above hasn’t dropped as much as it once did. But now consider that actually speed of manufacture isn’t the primary goal anymore. And now consider that something similar applies elsewhere too. I’m not sure whether this provides any grand solution or answer to the “productivity puzzle” economists fret about these days. But there may well be something there. We traded efficiency and cleanliness for speed, reducing our energy consumption along the way: but do all these qualitative improvements actually show up in the productivity data?
What you will find when you read Material World is that humankind is still making extraordinary technological leaps, but many of them are happening below the radar. There are plenty of challenges facing the world, not least climate change, but as each year goes by there is tangible evidence of progress, if only you look hard enough.
Even the world of car paint is not standing still. These days nearly all manufacturers do things pretty similarly. They all use electrodeposition and most of them use robots to do most of the car spraying. They are gradually beginning to explore replacing their gas ovens with electric ones to reduce the carbon emissions at plants.
The next big thing in the field is a technology which will allow carmakers to “print” paint on their vehicles, almost like inkjet printers. This will allow them to print custom designs, precise to the millimetre, on their cars and - even more importantly - to waste less ink. Chemicals companies are designing new paints with more vibrant finishes and fewer VOCs. For the time being most are still made from petrochemicals (in other words from oil and gas) but that too is set to change in the coming decades. These are exciting times in car paint - and the rest of the Material World.
If you’ve read this far then first off: thank you for proving my point that car paint is significantly more interesting than is often assumed. It’s one of many wormholes I found myself disappearing into while writing Material World. Please do share this with anyone you think might be interested. And if you have any thoughts/comments/corrections please do let me know below.
Many thanks to the car coatings team at Nissan UK who helped explain the modern process of car paint to me. For more on the chemicals industry, Fred Aftalion’s book is a good place to start. A couple of other interesting articles:
https://www.paint.org/coatingstech-magazine/articles/brief-history-automotive-coatings-technology/
I found this very interesting Ed. My husband works in R&D for cans, another unreported area. He started off on the coatings side and then moved to the actual cans. Again, a lot of the research nowadays is into making "greener" cans. We can take for granted picking up that can of beans or tuna in the supermarket but keeping the contents safe, the product affordable and better for the environment is a constant challenge.
Really interesting read, Ed, thx for sharing. I’m disappointed that car paint colours these days are so dull (is that driven by customers or manufacturers?), but you’ve shed some light on why more colours are available. I’d like to see more cars use the iridescent paints sported by TVRs - did they pop up in your research? Finally, you might be interested to know my previous company did some research that revealed yellow/orange cars are driven more quickly than any other colour. :-)
Cheers, Simon Gandy