Nobody said this would be easy
Across various sectors, businesses are realising that getting to net zero might be considerably harder than they initially assumed
You probably haven’t heard of Acrylonitrile Butadiene Styrene before but you’ve almost certainly played with it.
ABS is a tough thermoplastic, which is to say one of those plastics you can melt down and form back into other shapes again, and it’s the kind of thing you find in the handles of scissors or the frames of hard carry-on baggage cases. But probably its most iconic application is in the manufacture of Lego bricks.
Not all Lego pieces are made out of ABS. The Danish toy company uses a fair few other plastics in its sets: the baseplates (those big, flat knobbly boards) are moulded from high impact polystyrene. The gearwheels which you attach to wheels are polyamide, the small, flexible green pieces that look like plant stalks or flags are polyethylene, and so on and so on.
But the vast majority of Lego - more than 80 per cent - is those bricks you’ve doubtless played with and/or found yourself cursing as you accidentally step on top of them. And these ones? They’re all made from ABS.
There’s a reason Lego uses ABS. It’s incredibly durable, which means the pieces can be handed down from generation to generation. It can be moulded incredibly precisely, with tolerances of within four microns, meaning one brick fits neatly into another. Moreover not only is it exceptionally solid and workable, it also has pretty unbeatable “clutch power”, as the company calls it: the bricks stick together robustly but are also pretty easy to pull apart.
That Lego bricks are made of ABS is no accident. Its deployment in the 1960s was the culmination of years of experimentation. Back before that Lego used to make its main bricks from something called cellulose acetate, but CA bricks tended warp and deform over time, while their colour faded. ABS, in all its strong, clutchy, scratch-resistant glory, was the zenith - the ultimate Lego material.
But the catch here is that ABS is made from crude oil - well, strictly speaking from both oil and gas. Every kilogram of Lego blocks in your cupboard or on the toy store shelves began its life as two kilograms of crude oil.
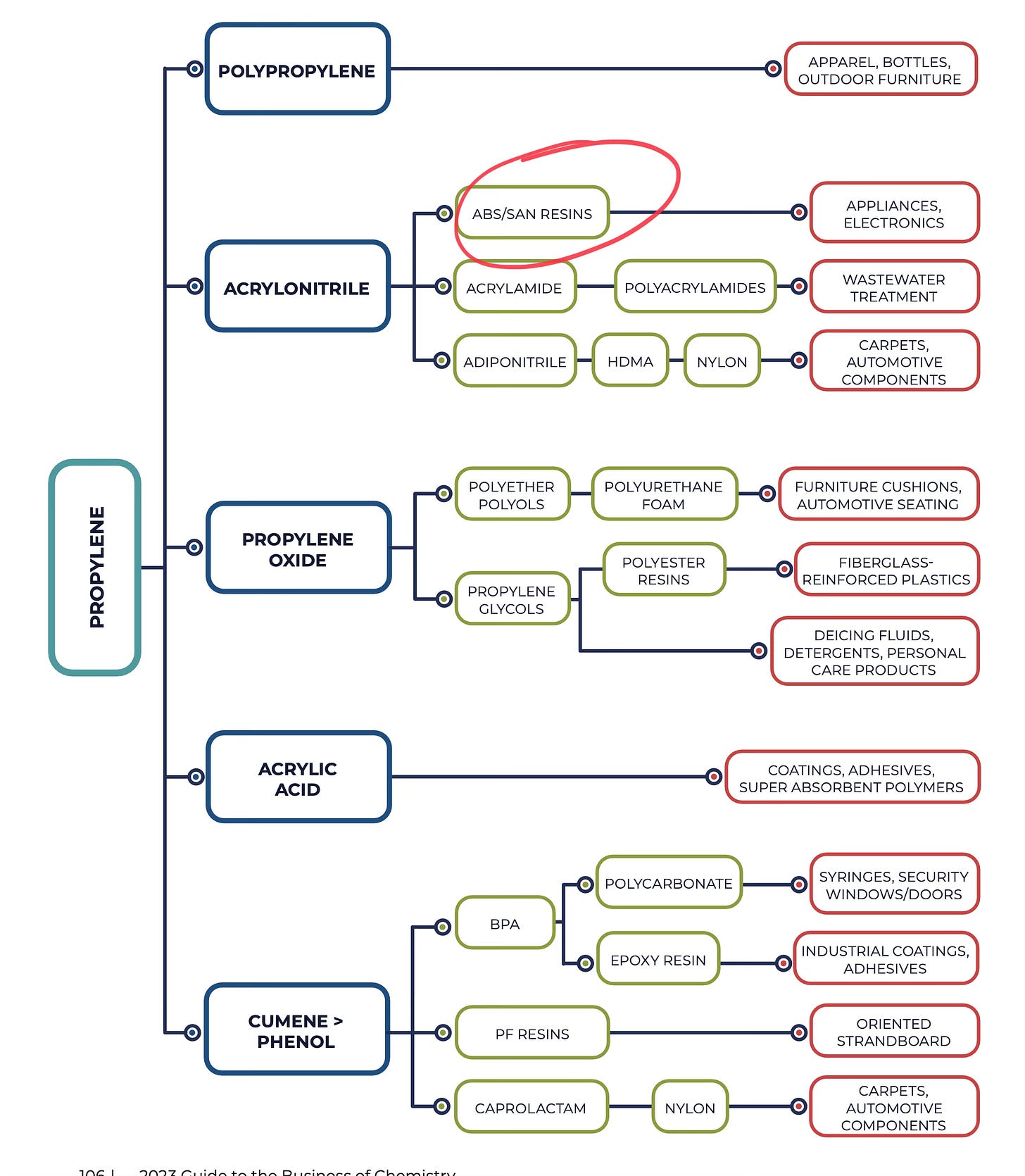
The acrylonitrile is made from the ethylene you find coming out of the crackers at oil refineries (much more on refineries - incredibly important places we rarely spend much time thinking about - in chapter 14 of Material World). Butadiene you get when you catalyse and dehydrogenate butane, while styrene - the same root chemical at the heart of polystyrene - comes from benzene. You get the picture… ABS - the Lego brick - is in some senses the quintessential petrochemical product.
Which is a problem if you have a commitment to sustainability and eliminating carbon emissions in the coming decades, as Lego does. So the plan, up until recently, was to replace ABS with an oil-free alternative. There was much fanfare, a couple of years ago, when Lego announced that it had a prototype replacement for ABS bricks it could make from recycled plastic bottles.
The issue, it turns out, is that recycled polyethylene terephthalate simply wasn’t quite as good as ABS. According to the Financial Times, Virgin RPET was far too soft, and turning it into something resembling ABS involved adding lots of extra ingredients as well as processing it and drying it, a highly energy-intensive process. So much extra work, in fact, that the carbon footprint of these “greener” Lego bricks would have been higher than the old oil-based ABS bricks.
So, says Lego, this particular plan has been ditched. ABS has had a stay of execution, and there’s a dawning realisation now that it might not be easily replaced. It might not be replaceable at all.
“In the early days, the belief was that it was easier to find this magic material or this new material” to solve the sustainability issue, the Lego chief executive Niels Christiansen told the FT. But “that doesn’t seem to be there. We tested hundreds and hundreds of materials. It’s just not been possible to find a material like that.”
Part of the problem here - one which crops up again and again throughout Material World - is that it turns out the suite of materials we tend to use these days are simply very good at doing what they do.
Kerosene is really, really hard to beat as a fuel for aviation. Methane is a brilliant source of the hydrogen you need to fix nitrogen from the atmosphere in order to make fertilisers. Concrete might not be the only strong building material, but it’s incredibly easy to lay and also phenomenally cheap - a large part of the explanation for how we’ve been able to urbanise and build enough accommodation for a growing global population.
It’s not that this stuff is necessarily impossible to replicate or even to beat. Not in the slightest. Consider electric cars: in certain respects, today’s EVs are considerably better than the petrol cars they’re replacing. While up to 80 per cent of the energy in petroleum is wasted, much of it coming out of the exhaust pipe as heat and fumes, the wagon-to-wheel efficiency of an electric car, using the best rare earth metal motor and advanced inverters, loses barely 20 per cent of the energy along the way.
Yes there are plenty of other question marks with EVs: for instance, how will we ramp up lithium production - not to mention copper and nickel and all the other metals we’ll need for this far more material-dense machines - without making them completely unaffordable? How can we mine all that stuff sustainably, given mining practices in many cases are very destructive and dirty? How can we build the grids we need so people can charge whenever or wherever they need, as easily as they can fill up their petrol cars today? Etcetera etcetera.
The point is: in most respects electric cars are a superior technology to what they’re replacing. Had we managed to invent lithium ion batteries back in the 1880s rather than the 1980s we’d probably always have been driving electric cars. But we didn’t, because lithium ion batteries were hard to make, so that had to wait until the modern era. Plenty more on that in chapters 16 and 17 of Material World by the way (excuse all these promotional bits but, well, no don’t, because persuading you to read the book is the whole point here).
But while in some cases, like electric cars, the tech now means the replacement for what came before is actually better, in many cases, it’s just really, really hard to improve on fossil fuel products.
Lego bricks are only the start of it. There’s an interesting scientific project underway here in the UK called Flue2Chem. Essentially, a group of scientists and businesses are attempting to map out the supply chain you’d need if you really were replacing the fossil carbons we use to make everyday products like packaging, paints, adhesives, textiles, drugs, fertilisers, insulation and cleaning products.
You might not think of laundry liquid as a fossil fuel product, and certainly some of the main elements come from elsewhere (for instance, salt! - see chapter 5 of Material World). But among the most important ingredients inside most detergents are a collection of molecules called surfactants. These are the clever chemicals which help prise dirt off from fabrics.
A typical surfactant is comprised of two parts - an oleophilic section which grips onto the dirt and a hydrophilic bit that dissolves in water. These chemicals are churned out in their millions from chemicals plants (about 17.6 million tonnes a year, equivalent to 44 million tonnes of carbon dioxide equivalent). Those chemicals come in turn from crude oil. So it’s a similar story to ABS.
Reading David Bott’s accounts of Flue2Chem’s experiments making surfactants from non-oil feedstocks (the plan is to make it from carbon dioxide sequestered from chimneys), a couple of things struck me. First, even for this comparatively simple molecule, the processes necessary are surprisingly complex. Second, we’re still very much in the early stages of working out how to do this.
Now, it’s worth saying there’s still plenty of time for Lego to reduce their carbon emissions and have more sustainable bricks. And while it looks like it’ll be yoked to ABS for the foreseeable future it still plans to be a net zero carbon emitter come 2050. And as it happens there is plenty of work underway to try to produce ABS (and its constituent parts) without quite as much carbon and from bio sources. And hey, it turns out there’s quite a lot of progress being made on this front too. So there is progress towards net zero. But no silver bullet (if that’s not too weird an analogy to use about something plastic).
All of this is a reminder of something rather important. Getting to net zero won’t be easy. There will be lots of false horizons - many products or breakthroughs that turn out to be considerably less straightforward than it looked. A lot of hype, in short. And a lot of hard work.
It feels right now as if we’re going through one of those humps. The share prices of many exciting tech firms which promised to solve this or that carbon problem have recently taken a tumble. Hope in some quarters has been replaced by depression or weariness.
Then again, we should hardly be surprised. The Material World is a place of both hope and despair. Because trying to reach net zero - trying to spark a fully-fledged Industrial Revolution - is really, really hard! It’s probably the single biggest economic challenge we’ve ever set ourselves as a species. So it won’t be solved easily. But the flip side of this is that the coming decades will be an exhilarating period, because millions of brains are now at work trying to solve some of these challenges - reimagining how we make the building blocks of civilisation, not to mention the building blocks of, well, Lego.
As always, a wonderfully insightful article.
But I hope you won’t mind my saying that there is another really important point about crude oil (haven’t got to that chapter yet, so forgive me if you cover it). That is that crude oil is a highly complex mixture of different compounds or fractions. We all know that. But we don’t often focus on the key implication, which is that so long as there is irreplaceable demand for one or two of those fractions that can’t be substituted by a non-fossil source, the oil will still be needed. And once drilled, it will still be separated into all of its constituent fractions. And then something will have to be done with the ones we don’t want (even if they now make up 90%+ of the mix). And the cheapest thing to do will almost always be either to use the other fractions as we do now or, gulp, to burn them (if we can). Even if you can pump them back underground, you will have dramatically altered the economics of the product you still need and made it massively more expensive....
Sorry if this is obvious to you, but I’m convinced that it’s not obvious to most people.
' Using the best rare earth metal motor' - of course the best motors today do not need to use rare earth metals. The sustainable solution is to use an alternative technology from Advanced Electric Machines based in Washington, United Kingdom. https://advancedelectricmachines.com/ This requires more advanced electronics and can also be designed without the use of copper.